RESISTANCE WELDING
What is RESISTANCE WELDING?
Resistance seam welding is a type of resistance welding process used to join two overlapping metal sheets along a continuous seam. It is commonly employed in various industries, including automotive, aerospace, and appliance manufacturing. In resistance seam welding, the two metal sheets are clamped together between two electrodes, and an electric current is passed through the joint area. The heat generated by the resistance to the electric current causes the metal to soften and fuse, creating a welded seam.
Here are the key features and steps involved in resistance seam welding:
1. Equipment: Resistance seam welding requires specialized welding equipment that consists of two rotating copper electrodes. These electrodes apply pressure to the metal sheets and conduct the electric current necessary for welding.
2. Sheet Preparation: The metal sheets to be joined are typically overlapped with a specific overlap width, which ensures adequate contact area for effective welding. The sheets are cleaned and aligned properly before the welding process.
3. Clamping and Welding: The metal sheets are securely clamped between the two rotating electrodes. The electrodes exert pressure on the sheets, ensuring good contact and minimizing the resistance between them. An electric current is then passed through the electrodes and the joint area between the sheets.
4. Heating and Fusion: The electric current generates resistance heating at the contact points between the metal sheets. This causes the metal to soften and reach the welding temperature. The heat generated by the resistance causes the overlapping edges to fuse together, forming a continuous seam.
5. Weld Formation: As the electrodes move along the joint, the molten metal solidifies, resulting in a welded seam. The welding parameters, such as current, time, and electrode speed, are carefully controlled to achieve the desired weld quality and strength.
6. Cooling and Solidification: After the electrodes pass through the entire joint, the welded seam cools and solidifies, creating a strong and durable bond between the metal sheets.
Resistance seam welding offers several advantages, including:
- High-speed welding: It allows for rapid and continuous welding of long seams, making it suitable for high-volume production.
- Strong and reliable welds: The fusion of overlapping edges creates a robust and consistent weld joint.
- Efficient heat generation: Resistance heating focuses on the joint area, minimizing heat dissipation and reducing the potential for distortion.
- Cost-effective: Resistance seam welding is a relatively cost-effective welding process compared to some other methods.
- Versatile: It can be applied to a variety of metals, including steels, stainless steels, and aluminum.
Resistance seam welding finds application in various industries where continuous seams are required, such as automotive body panels, fuel tanks, air conditioning ducts, and appliances.
Benefits
Resistance seam welding offers several key benefits that make it a preferred welding method in various industries. Here are some of the key benefits of resistance seam welding:
1. Efficiency and High Productivity: Resistance seam welding is a high-speed welding process that allows for the continuous welding of long seams. It offers high productivity and efficiency, making it suitable for high-volume production.
2. Strong and Durable Welds: Resistance seam welding produces robust and reliable welds. The overlapping edges of the workpieces are fused together, creating a continuous and secure weld seam with good strength and integrity.
3. Enhanced Aesthetics: Resistance seam welding produces clean and uniform welds with minimal surface distortion. This results in aesthetically pleasing welds, which is especially important in applications where the appearance is a key consideration.
4. Cost-Effectiveness: Resistance seam welding is a relatively cost-effective welding process. It requires simple equipment, minimal tooling, and consumes less energy compared to other welding methods. The high productivity of the process also contributes to cost savings.
5. Versatility: Resistance seam welding is versatile and can be applied to a wide range of materials, including steels, stainless steels, and aluminum alloys. It is suitable for joining various sheet metal components used in industries such as automotive, aerospace, appliances, and HVAC systems.
6. Heat Control: Resistance seam welding concentrates heat generation to the joint area, minimizing heat dissipation and reducing the risk of distortion or damage to the surrounding material. This precise heat control helps maintain the structural integrity of the workpiece.
7. Process Stability and Control: Resistance seam welding allows for precise control over welding parameters such as current, voltage, and electrode speed. This facilitates consistent weld quality and ensures repeatability in production.
8. Seam Integrity: The continuous nature of the seam welding process ensures consistent weld quality along the entire length of the seam. This leads to reliable joint strength and improved leak-tightness in applications requiring sealed or hermetic connections.
9. Low Heat Input: Compared to some other welding methods, resistance seam welding introduces relatively low heat input to the workpiece. This reduces the risk of distortion, warping, or metallurgical changes in the material, particularly in thin-gauge or heat-sensitive materials.
10. Safety: Resistance seam welding offers a safe welding process as it does not involve an open arc or the use of consumables like filler materials. This minimizes the risk of spatter, sparks, or fumes, improving safety conditions for operators.
These benefits make resistance seam welding a reliable and efficient method for joining sheet metal components, providing strong, durable welds with high productivity and cost-effectiveness.
Design specifications
When designing for resistance seam welding, there are several important specifications to consider to ensure successful and efficient welding. Here are some key design considerations and specifications for resistance seam welding:
1. Material Selection: Identify the appropriate materials for resistance seam welding based on their weldability and compatibility with the process. Consider factors such as conductivity, thickness, and surface condition. Common materials for resistance seam welding include steels, stainless steels, and aluminum alloys.
2. Joint Design: Design the joint configuration to facilitate effective welding. The joint type, overlap width, and edge preparation should be specified to ensure proper contact and alignment during welding. Adequate surface preparation, such as cleaning and degreasing, is crucial to ensure proper electrode-to-workpiece contact.
3. Electrode Design: Specify the design and material of the electrodes used in resistance seam welding. Electrodes should be made of a conductive material, such as copper, to ensure efficient heat transfer. Consider the electrode shape, size, and surface finish to achieve consistent contact and minimize electrode wear.
4. Clamping and Pressure: Define the clamping mechanism and pressure applied during welding. Proper clamping ensures sufficient contact between the workpieces and electrodes, enabling effective heat generation and fusion. The clamping force should be sufficient to maintain consistent pressure throughout the welding process.
5. Welding Parameters: Specify the welding parameters, including current, voltage, time, and electrode speed. These parameters determine the heat input and fusion characteristics during welding. Optimal parameter selection depends on the material thickness, conductivity, and desired weld quality. Close collaboration with welding experts and process trials can help determine the appropriate parameters.
6. Quality Control: Define the required quality control measures for resistance seam welding. This may include inspections for weld integrity, dimensional accuracy, surface finish, and any specific defect criteria. Identify non-destructive testing methods, such as visual inspection or ultrasonic testing, to ensure the weld quality meets the specified requirements.
7. Weld Strength and Integrity: Specify the required strength and integrity of the weld. This includes determining the minimum tensile strength, shear strength, or other mechanical properties necessary for the application. Consider factors such as joint design, electrode configuration, and welding parameters to ensure the weld meets the desired strength criteria.
8. Production Volume: Consider the anticipated production volume or quantity of parts to be welded using resistance seam welding. This can influence factors such as equipment selection, automation, and production efficiency considerations.
9. Weld Seam Accessibility: Account for the accessibility of the weld seam during the welding process. Ensure that the electrode design and equipment allow for easy access to the intended welding areas.
10. Weld Integrity Testing: Specify the required testing methods or destructive testing procedures to verify the integrity and strength of the weld. This may include destructive testing, such as peel or tensile testing, to assess the weld strength.
These design specifications for resistance seam welding are crucial to ensure efficient and consistent welding outcomes. Collaborating with experienced welding engineers and manufacturers can help optimize the design and welding parameters for the specific application.
APPLICATIONS
Resistance seam welding finds application in various industries for joining sheet metal components along continuous seams. Some common applications of resistance seam welding include:
1. Automotive Industry: Resistance seam welding is extensively used in the automotive sector for joining components such as vehicle bodies, fuel tanks, exhaust systems, door panels, and seat frames. It provides strong and durable welds that contribute to the structural integrity and safety of vehicles.
2. Aerospace Industry: Resistance seam welding is employed in the aerospace industry for joining sheet metal components used in aircraft structures, including fuselage panels, wings, and fuel tanks. The process ensures reliable and high-strength welds that meet stringent quality and performance standards.
3. Appliance Manufacturing: Resistance seam welding is utilized in the production of home appliances such as refrigerators, washing machines, dryers, and HVAC systems. It is employed to join components like cabinets, panels, and tubs, ensuring secure and leak-tight seals.
4. HVAC and Ducting Systems: Resistance seam welding is commonly used in the fabrication of heating, ventilation, and air conditioning (HVAC) systems. It enables the joining of ducts and components, ensuring airtight seals and efficient airflow.
5. Furniture Manufacturing: Resistance seam welding finds application in the production of furniture, especially metal furniture. It is used to join components like frames, supports, and brackets, providing strong and reliable connections.
6. Electrical Enclosures: Resistance seam welding is employed in the manufacturing of electrical enclosures and cabinets used in industries such as power distribution, telecommunications, and control systems. It ensures robust and secure joints for housing sensitive electronic equipment.
7. Industrial Equipment: Resistance seam welding is utilized in the fabrication of various industrial equipment, including cabinets, panels, and frames. It provides strong and durable welds that can withstand the demanding conditions of industrial environments.
8. Storage Tanks: Resistance seam welding is employed in the production of storage tanks for liquids or gases. It ensures leak-tight and secure joints for applications such as fuel storage, chemical storage, and industrial processing.
These are just a few examples of the applications of resistance seam welding. The process is versatile and widely used in industries where continuous and reliable welds are required for joining sheet metal components.
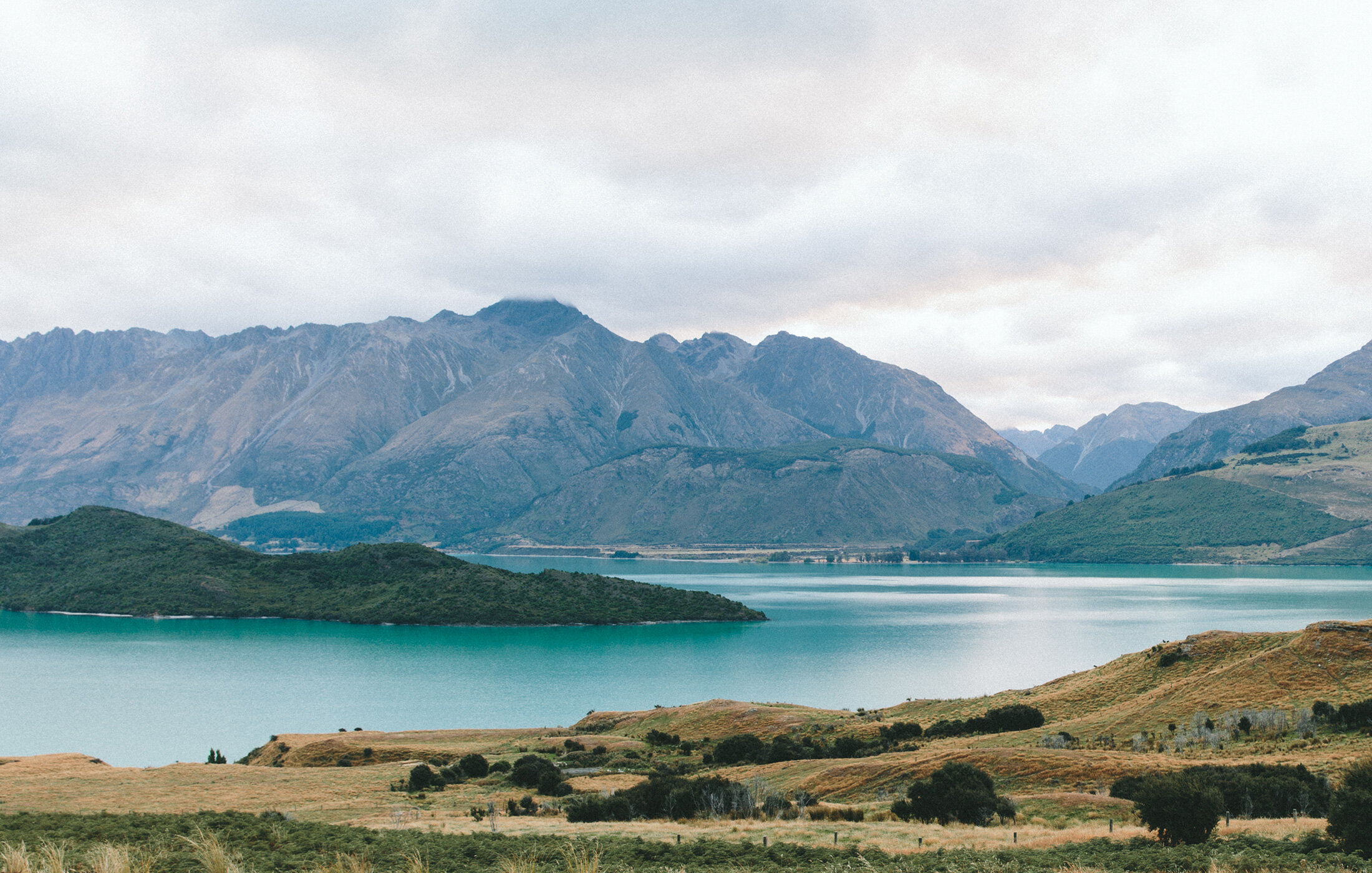
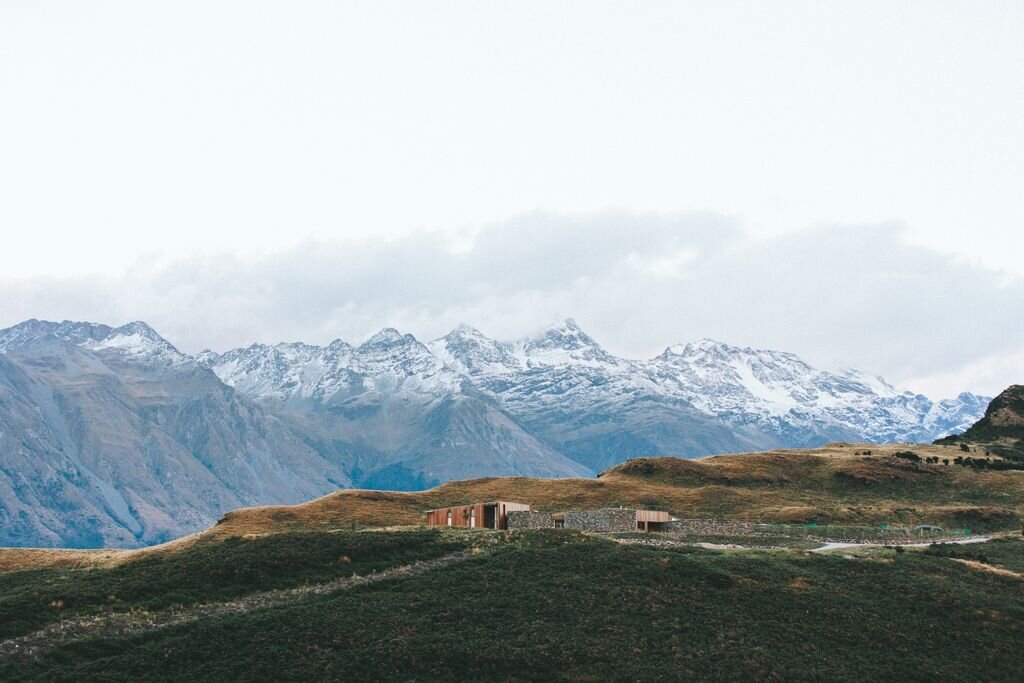
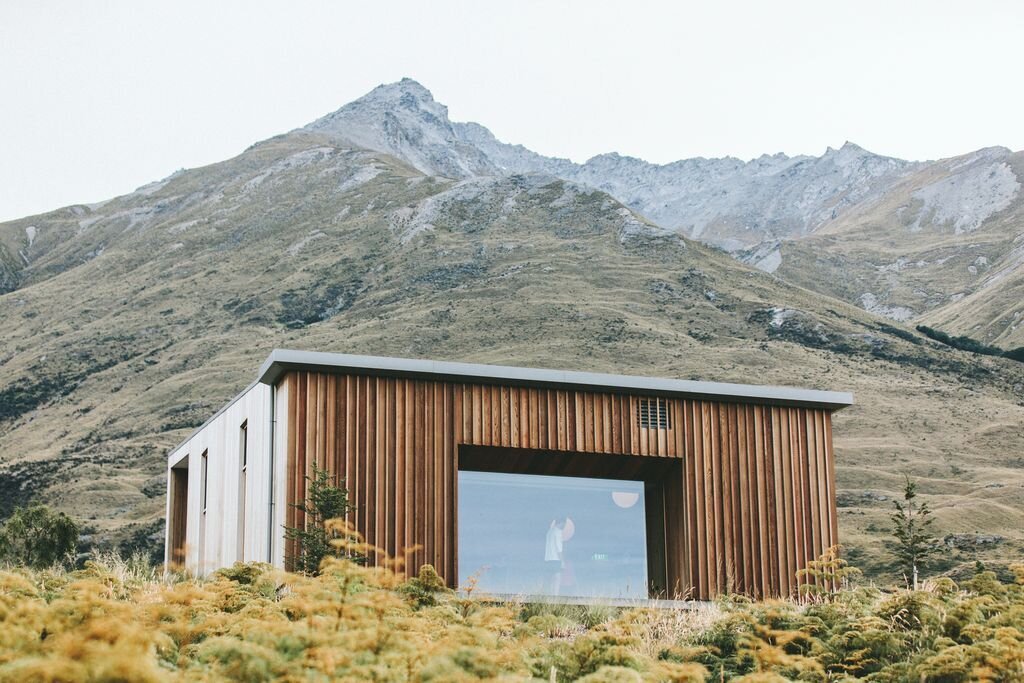
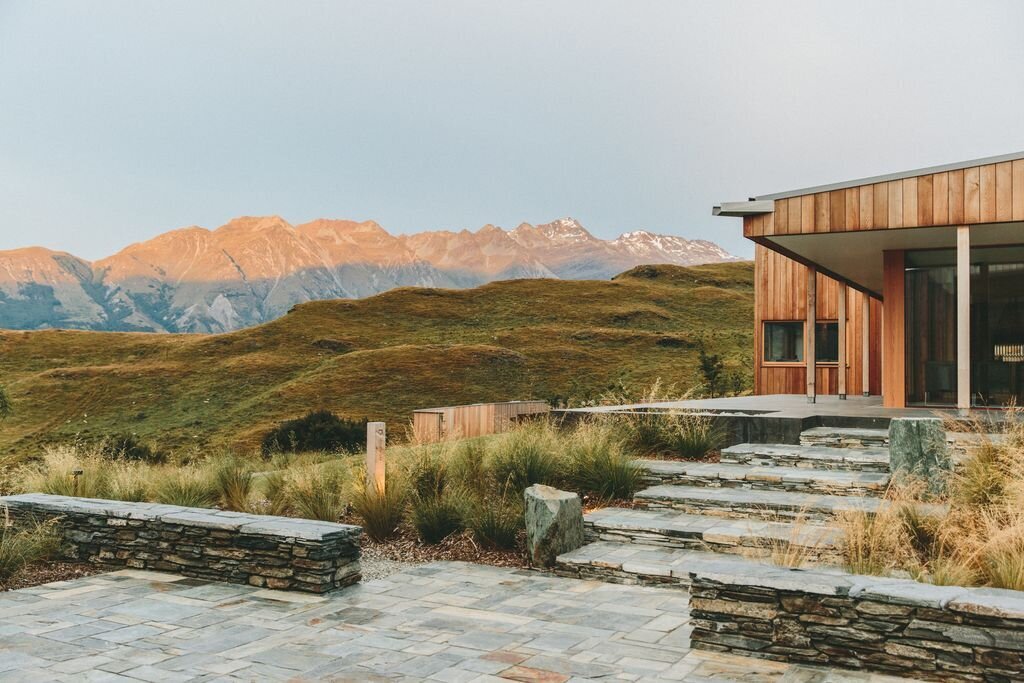
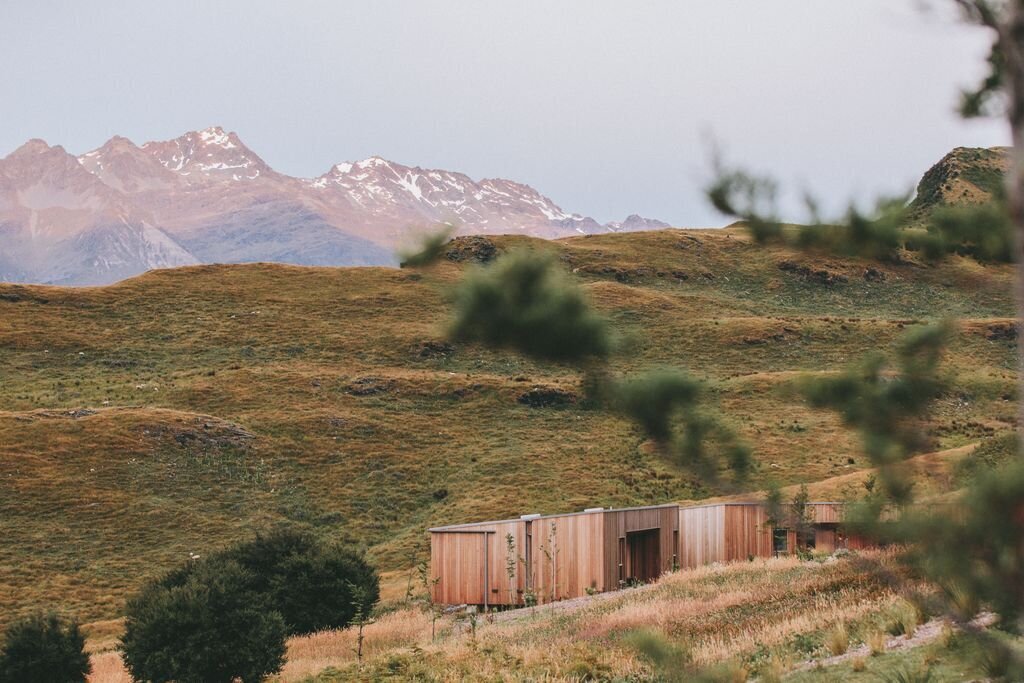
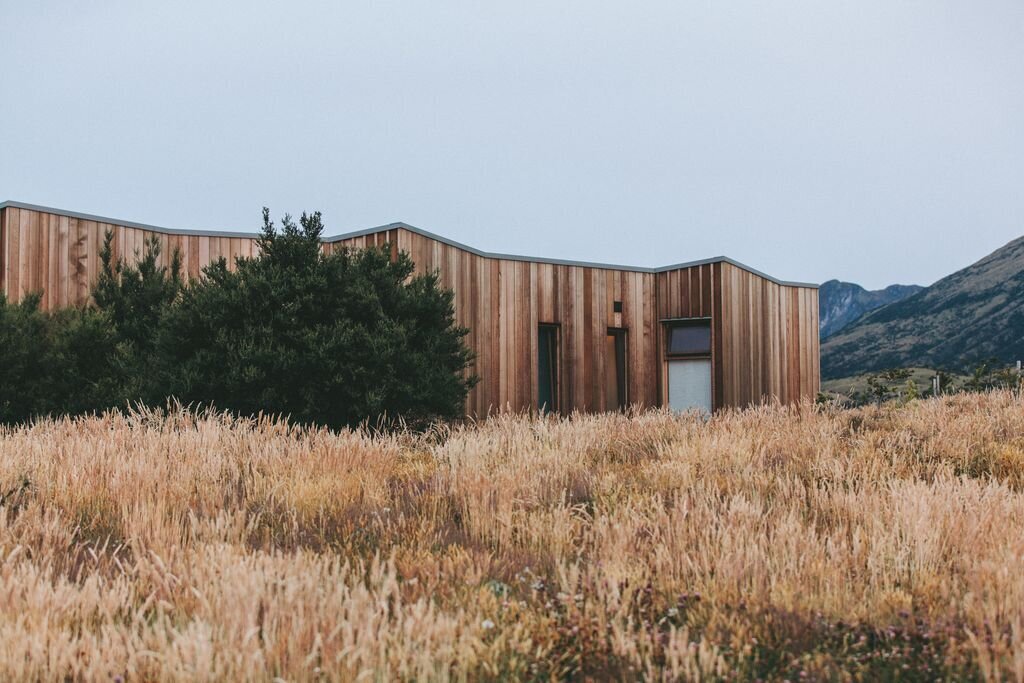