EDM
What is EDM?
EDM stands for Electrical Discharge Machining. It is a machining process that utilizes electrical discharges (sparks) to remove material from a workpiece. EDM is also known as spark machining or spark eroding.
In EDM, a workpiece and an electrode (also known as a tool or a die) are submerged in a dielectric fluid, typically oil or deionized water. The workpiece and electrode are connected to a power supply, creating a potential difference between them. When the voltage is applied, a series of electrical discharges occur between the workpiece and the electrode. These discharges generate intense heat, which melts and vaporizes the material, thereby removing it from the workpiece.
EDM is commonly used for machining complex shapes, hardened materials, and materials that are difficult to machine using conventional methods. It is particularly useful for producing molds, dies, and tooling for various industries, including aerospace, automotive, and medical.
There are two primary types of EDM: wire EDM (WEDM) and sinker EDM (also known as plunge EDM or ram EDM). In wire EDM, a thin wire serves as the electrode, while in sinker EDM, a specially shaped electrode is used to create cavities or holes in the workpiece.
EDM offers high precision, excellent surface finish, and the ability to machine intricate details. However, it is a relatively slow process compared to other machining methods.
Benefits
Electrical Discharge Machining (EDM) offers several benefits that make it a valuable manufacturing process in various industries. Here are some key benefits of EDM:
1. Precision: EDM is known for its exceptional precision in machining complex shapes and tight tolerances. It can produce intricate details and features with high accuracy, allowing for the manufacturing of parts with precise dimensions and geometric complexity.
2. Versatility: EDM can be used to machine a wide range of conductive materials, including hardened steels, exotic alloys, and heat-resistant materials. It is particularly effective for materials that are difficult to machine using conventional methods. This versatility makes EDM suitable for diverse applications across industries.
3. No Tool Contact: Unlike traditional machining processes, EDM does not involve direct physical contact between the cutting tool and the workpiece. Instead, it uses electrical discharges to erode the material. This eliminates the risk of tool wear, reducing the need for frequent tool changes and enhancing overall process stability.
4. Complex Geometries: EDM enables the production of intricate and complex part geometries that may be challenging or impossible to achieve with conventional machining methods. It allows for the machining of internal features, sharp corners, fine details, and small radii, meeting the demands of industries such as aerospace, automotive, and medical.
5. Heat-Affected Zone Control: EDM is a non-thermal cutting process, meaning it generates minimal heat during machining. This reduces the likelihood of thermal distortion or damage to the workpiece, making it suitable for heat-sensitive materials and maintaining the material's structural integrity.
6. Surface Finish: EDM can achieve excellent surface finishes, even on complex shapes and hardened materials. The absence of cutting forces and the ability to control the spark parameters allow for the production of smooth surfaces with low surface roughness, reducing the need for secondary finishing operations.
7. Material Hardness: EDM can efficiently machine materials with high hardness, such as tool steels and carbides. It is particularly beneficial for producing molds, dies, and tooling that require exceptional hardness and wear resistance.
8. Low Forces: EDM exerts very low cutting forces on the workpiece, reducing the risk of part distortion or deflection. This makes it suitable for delicate or thin-walled components that may be susceptible to deformation during machining.
9. Automation and Unattended Operation: EDM can be automated and programmed to run unattended, increasing productivity and reducing labor costs. The ability to run long machining cycles without operator intervention makes it suitable for lights-out manufacturing and improving overall production efficiency.
10. Reduced Tooling Costs: Since EDM does not involve physical contact with the workpiece, the electrode wear is the primary tooling cost. Depending on the application, electrodes can be made from inexpensive materials, reducing tooling expenses.
It's important to note that while EDM offers numerous advantages, it also has some limitations, such as slower machining speeds compared to conventional methods and the inability to machine non-conductive materials. Therefore, it is crucial to consider the specific requirements of the application when deciding whether EDM is the appropriate manufacturing process.
Design specifications
The design specifications for EDM (Electrical Discharge Machining) may vary depending on the specific application and requirements. However, here are some common design considerations and specifications for EDM:
1. Material Compatibility: EDM can be used to machine a wide range of conductive materials, including metals and alloys. The design specification should include the material type and its properties, such as hardness, conductivity, and thermal characteristics.
2. Part Geometry: The desired shape, dimensions, and features of the part or workpiece should be defined in the design specifications. This includes considerations for complex geometries, internal features, tight tolerances, and surface finish requirements.
3. Electrode Design: The electrode, which is an essential component in EDM, needs to be designed according to the desired shape and features to be machined. The electrode material, size, and configuration should be specified, considering factors such as wear resistance, electrical conductivity, and ease of manufacturing.
4. Tolerances: The desired dimensional tolerances for the machined part should be clearly defined in the design specifications. This includes specifications for linear dimensions, angles, surface roughness, and positional accuracy.
5. EDM Parameters: The design specifications may include specific EDM process parameters, such as pulse duration, current, voltage, gap distance, flushing rate, and dielectric fluid type. These parameters can be tailored based on the material, desired surface finish, and machining efficiency requirements.
6. Surface Finish: The required surface finish for the machined part should be specified. This includes parameters such as Ra (roughness average) or specific surface roughness requirements.
7. Production Volume: The anticipated production volume or quantity of parts to be manufactured using EDM may influence the design specifications. It can impact factors such as tooling design, electrode wear, and production time.
8. Inspection and Quality Control: The design specifications should include provisions for inspection methods and quality control processes to ensure the produced parts meet the required specifications and standards.
These are some general design considerations and specifications for EDM. It is crucial to consult with experienced EDM operators and manufacturers to optimize the design specifications based on the specific application and production requirements.
APPLICATIONS
Electrical Discharge Machining (EDM) finds application in various industries and manufacturing processes. Some common applications of EDM include:
1. Mold and Die Making: EDM is widely used in mold and die making for industries such as automotive, aerospace, and plastics. It allows for the precise machining of complex shapes, cavities, and details required for molds and dies used in injection molding, metal stamping, and other manufacturing processes.
2. Aerospace Industry: EDM is employed in the aerospace industry for manufacturing turbine blades, engine components, and intricate parts that require high precision and tight tolerances. It enables the machining of difficult-to-cut materials like superalloys.
3. Medical Device Manufacturing: EDM is utilized in the production of medical devices and implants. It can create intricate features, such as small holes, notches, and grooves in materials like titanium and stainless steel, ensuring precise fit and functionality.
4. Tool and Die Manufacturing: EDM is extensively used for producing various cutting tools, such as drills, end mills, and inserts. It allows for the creation of complex tool geometries and sharp edges with high precision, enhancing cutting performance and durability.
5. Electronics Industry: EDM is employed in the manufacturing of electronic components like connectors, micro-molds for plastic parts, and intricate metal parts used in circuit boards. It helps achieve the required precision and miniaturization necessary for electronic devices.
6. Automotive Industry: EDM is utilized in the automotive sector for manufacturing components such as gears, transmission parts, fuel injection nozzles, and engine components. It enables the production of high-precision parts with complex shapes and tight tolerances.
7. Prototype Development: EDM is often used in the prototyping phase of product development, allowing designers to quickly create prototypes of intricate parts for testing and evaluation before mass production.
8. Jewelry Manufacturing: EDM is employed in the jewelry industry to create intricate designs, patterns, and engravings on precious metals. It enables precise and detailed customization of jewelry pieces.
These are just a few examples of the wide range of applications for EDM. The versatility, precision, and capability to machine difficult materials make EDM a valuable technology in various industries where complex shapes, tight tolerances, and fine surface finishes are required.
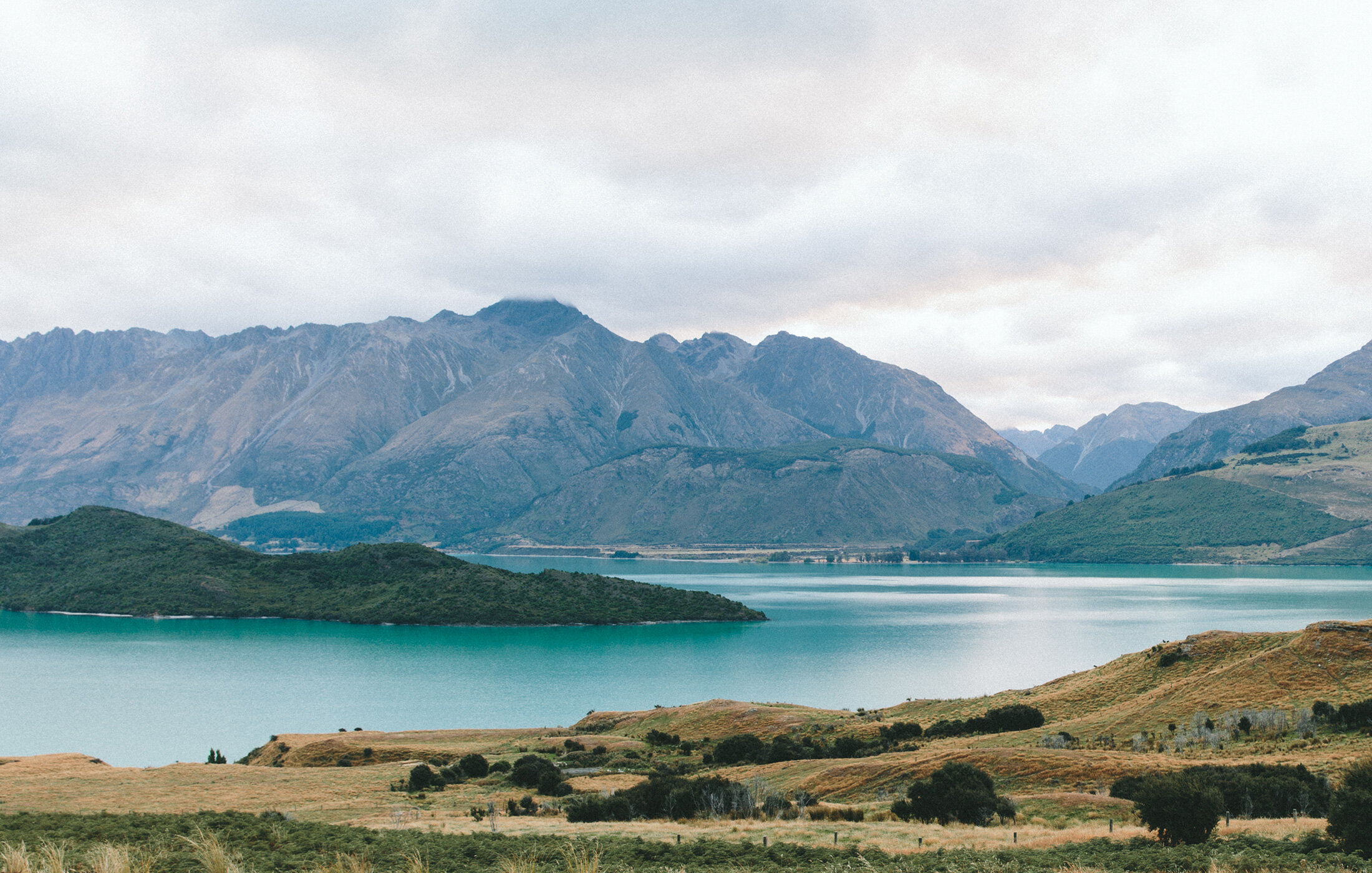
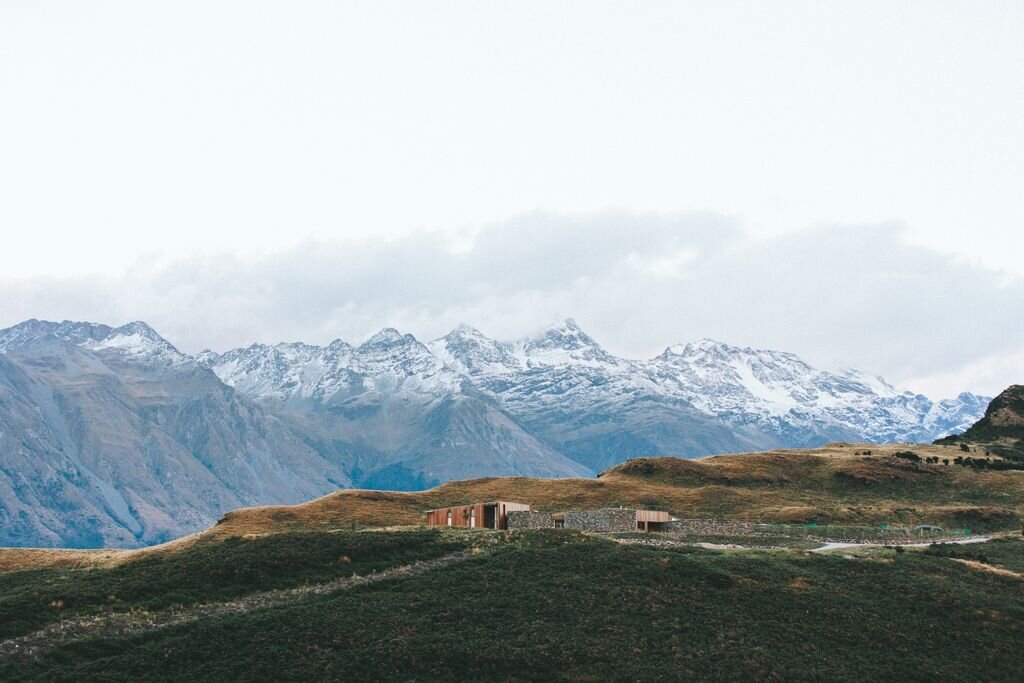
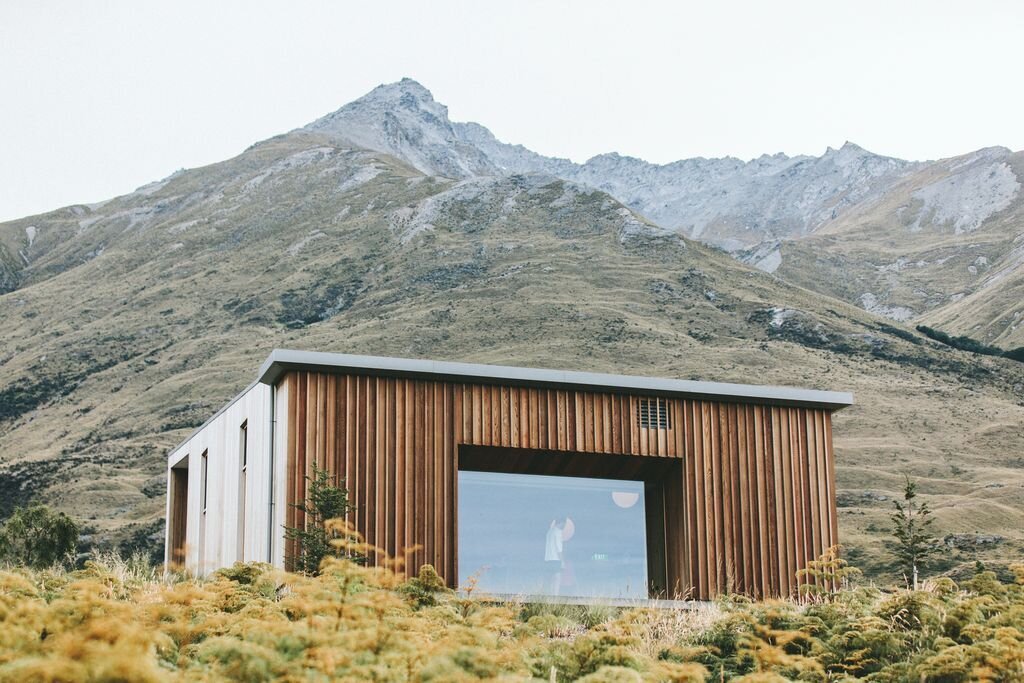
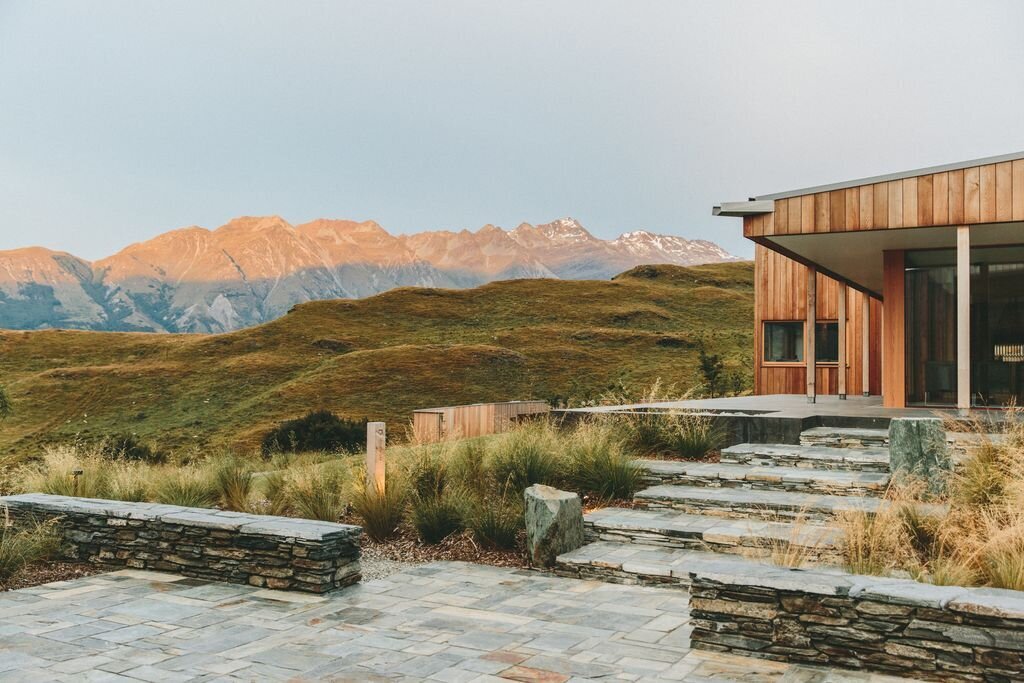
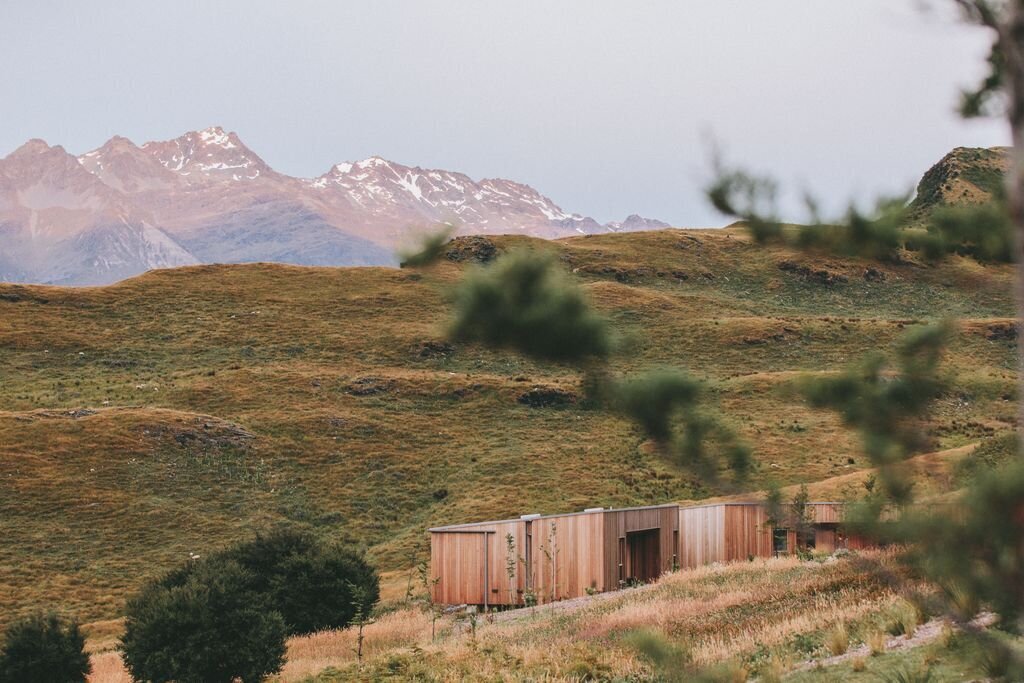
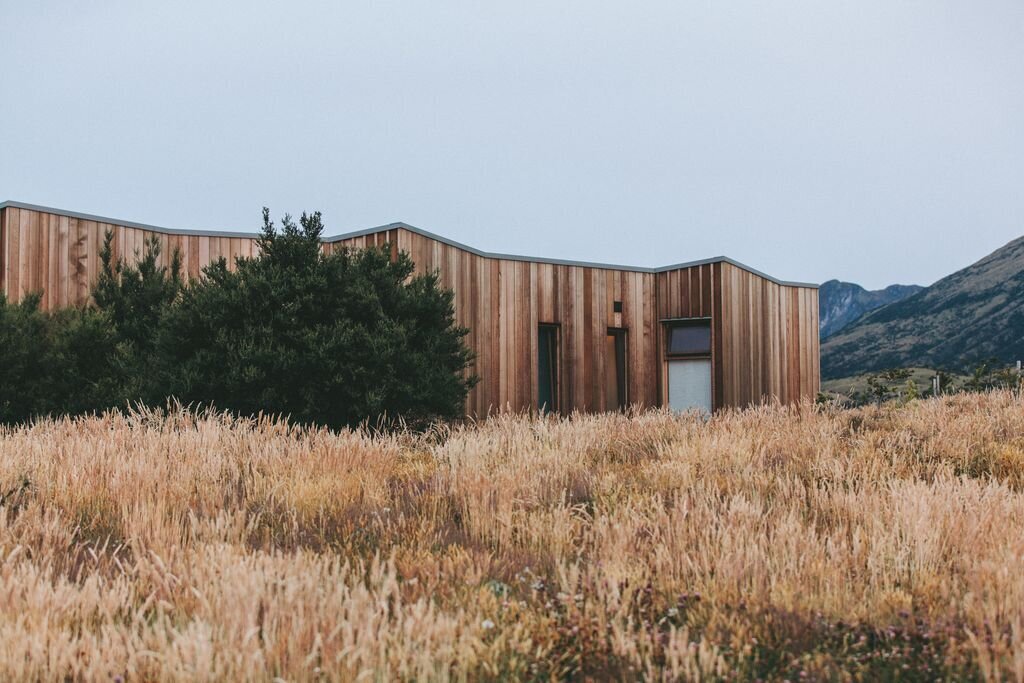